Blog
When practiced consistently, 5S becomes more than a tool—it becomes a habit that shapes how employees think and behave.
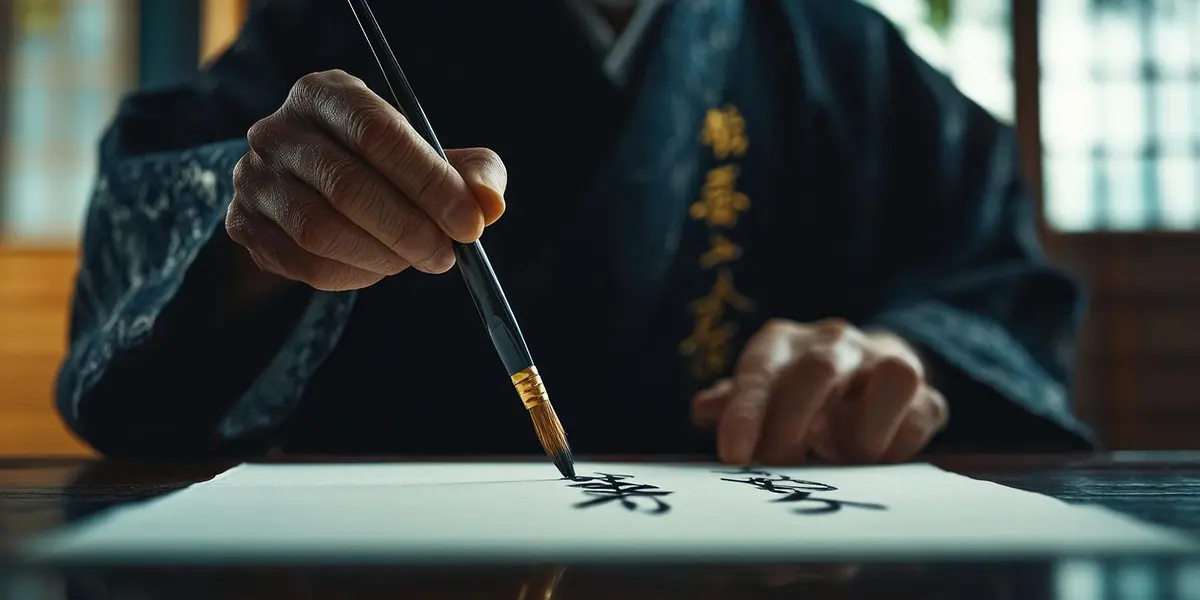
May 12, 2025
By
Kamran Awan
Category
Business
Introduction to 5S methodology
Origin and history of 5S
The 5S methodology traces its roots back to post-World War II Japan, specifically within the Toyota Production System (TPS). It was initially designed to improve workplace efficiency and safety through a simple but powerful system of organisation. The goal was to streamline processes, reduce waste, and create a clean and productive environment where work could flow more efficiently.
Developed as a cornerstone of lean manufacturing, 5S was not just a method; it became a cultural philosophy. Toyota's success eventually drew global attention, and the 5S system began spreading across various industries worldwide, far beyond manufacturing. Today, it's applied in healthcare, education, office settings, hospitality, and even personal productivity systems.
What makes 5S unique is its simplicity and universal applicability. It doesn't require expensive tools or technologies. Instead, it calls for a mindset shift, emphasising discipline, attention to detail, and respect for the workplace. When practiced consistently, 5S becomes more than a tool—it becomes a habit that shapes how employees think and behave.
What does 5S stand for?
The term "5S" stands for five Japanese words: Seiri, Seiton, Seiso, Seiketsu, and Shitsuke. In English, these roughly translate to:
- Sort (Seiri) – Remove unnecessary items from the workplace.
- Set in Order (Seiton) – Arrange items so they are easy to use and find.
- Shine (Seiso) – Keep the workplace clean and tidy.
- Standardise (Seiketsu) – Create standards and rules for maintaining organisation.
- Sustain (Shitsuke) – Make 5S a long-term habit through discipline and commitment.
The core philosophy behind 5S
At its core, 5S is about workplace efficiency, safety, and continuous improvement. But more than that, it's a cultural transformation. 5S encourages employees to take ownership of their environment. It teaches that a clean, organised workspace reflects the quality and discipline of the team working there.
The underlying philosophy of 5S is rooted in Kaizen, the Japanese principle of continuous improvement. Unlike one-off projects or reactive measures, 5S promotes a proactive, consistent approach to identifying inefficiencies and correcting them. When everyone in the organisation adopts the 5S mindset, it creates a ripple effect that enhances productivity, reduces frustration, and elevates the customer experience.
It's also worth noting that 5S fosters teamwork and accountability. Each employee plays a part in maintaining the standards, and over time, this builds a stronger, more cohesive work culture.
Step-by-step breakdown of the 5S principles
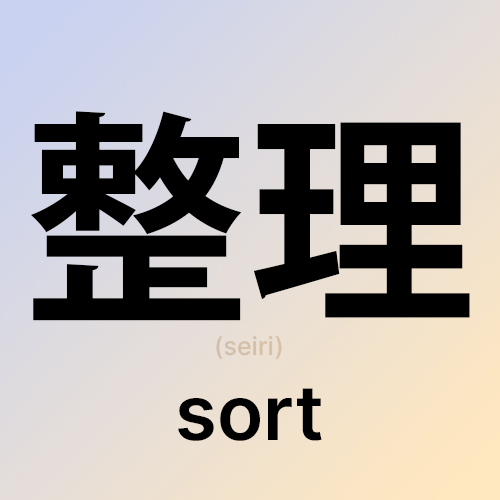
Sort (seiri) – Eliminate what you don't need
The first step in the 5S journey is to Sort. This means identifying and removing all unnecessary items from the workplace—anything that does not serve an immediate purpose or is used infrequently.
Imagine walking into a cluttered office or workshop. You see unused tools, old paperwork, broken equipment, and random items stuffed in drawers. This kind of clutter creates distractions, wastes time, and even poses safety hazards. That's where Sort comes in.
By carefully evaluating every item in your workspace, you can categorise what to keep, what to store elsewhere, and what to discard. It's a purge process that lightens the load, both physically and mentally.
Real-World Examples of "Sort" in Action:
- In a hospital setting, unused or expired medical supplies are regularly removed from patient care areas.
- In a warehouse, excess inventory is relocated or sold off to create more space for essential goods.
- In a digital workspace, outdated files and software are deleted or archived to improve system speed and clarity.
The result? A cleaner, more focused environment where only essential tools and materials remain.
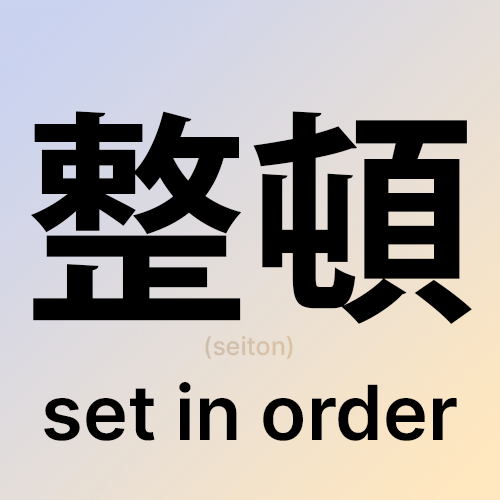
Set in Order (seiton) – Organise for efficiency
Once the unnecessary items are removed, the next step is Set in Order. This is all about arranging tools, materials, and equipment so that everything has a designated place—and more importantly, that every item is easy to access and return.
Think of it like organising your kitchen. Would you keep your cooking utensils in a random drawer far from the stove? Of course not. The same logic applies in the workplace.
Start by analysing your workflows. Which tools are used most frequently? Where should they be placed for maximum efficiency? The idea is to reduce movement, eliminate searching time, and speed up processes.
Tools and Techniques for Effective Organisation:
- Shadow boards: Tool outlines on boards that show exactly where each item belongs.
- Labelling systems: Clear labels on shelves, bins, and drawers.
- Colour coding: Visual cues that differentiate zones, equipment, or materials.
- Storage bins and racks: Modular solutions that keep small parts or files tidy.
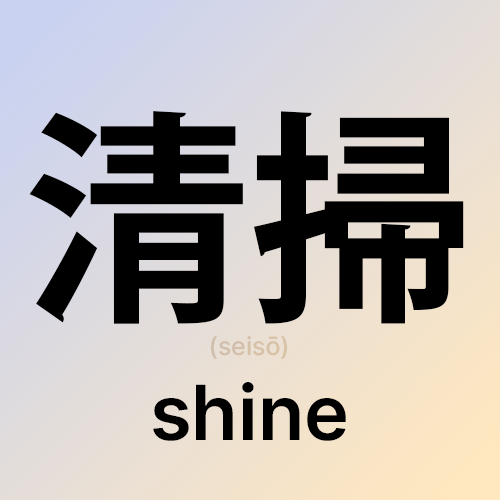
Shine (seisō) – Clean the workplace
Cleaning isn't just about aesthetics—it's about functionality and pride. Shine, the third S, is all about maintaining a clean and safe work environment. That includes wiping down surfaces, inspecting equipment, and removing dirt or hazards.
You might think cleaning is a janitorial duty, but in 5S, it's everyone's responsibility. Daily cleaning routines not only keep things tidy but also help spot problems early—like oil leaks, frayed wires, or malfunctioning machinery.
Establishing a Cleaning Routine:
- Assign cleaning zones and rotate responsibilities.
- Integrate cleaning into daily workflows.
- Use checklists to ensure nothing is overlooked.
- Celebrate "clean desk" days or conduct weekly clean-up drives.
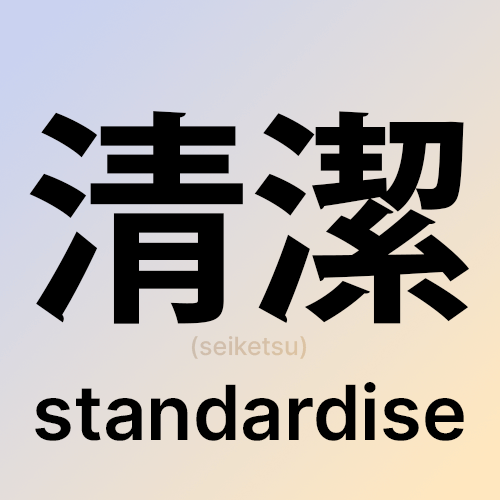
Standardise (seiketsu) – Create consistency
Once your workspace is sorted, organised, and clean, the next step is Standardise. This is where you create rules, routines, and procedures that ensure the first three S's (Sort, Set in Order, Shine) are maintained consistently over time.
Think of standardisation as turning good habits into a company-wide culture. Without it, all the work done in the previous steps can quickly fall apart. Things slip back into disorganisation, clutter returns, and cleaning routines fade. Standardising locks in your progress.
To achieve this, you'll want to develop and document best practices for every area of the workplace. This can include:
- Standard Operating Procedures (SOPs)
- Visual guides and signage
- Checklists for daily, weekly, and monthly tasks
- Role-based responsibilities for maintaining 5S
One of the best ways to maintain standardisation is through visual controls—easy-to-understand cues that guide behaviour. These can be as simple as coloured floor tape to mark pathways, diagrams showing how workstations should be arranged, or posted reminders about inspection checklists.
Visual cues eliminate guesswork and create a shared understanding among all team members. They also make training new employees easier because the expectations are literally right in front of them.
Don't forget to involve your team in this process. Get their input when creating SOPs and standards. After all, they're the ones doing the work, and their buy-in is crucial for lasting change. Standardisation should never feel like micromanagement—it's about making the best way the easiest way.
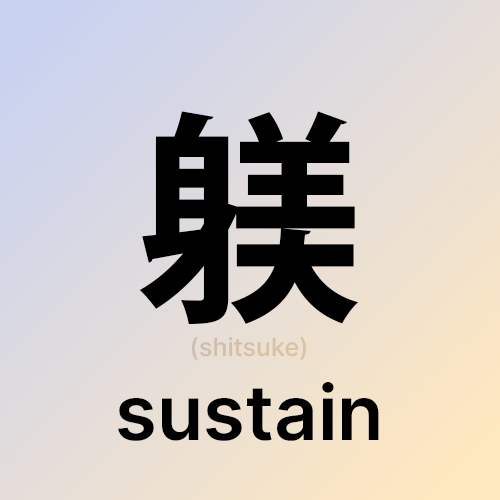
Sustain (shitsuke) – Maintain the discipline
The final and arguably most difficult stage is Sustain. This is where the rubber meets the road. You've cleaned and organised the workspace, set up standards—but can you stick with it?
Sustain is about turning 5S into a long-term habit. It's where you develop the discipline to maintain what you've built. Without this phase, the entire system will collapse over time. That's why "Sustain" isn't just a task—it's a mindset.
The key here is reinforcement. Regular training, daily check-ins, and visible leadership support all help to embed 5S into your workplace culture.
Training and Culture Development:
- Schedule 5S refresher training every quarter.
- Recognise and reward employees who exemplify 5S principles.
- Include 5S goals in performance reviews.
- Appoint 5S champions or team leaders to drive engagement.
Remember, discipline doesn't happen by accident. It's cultivated by consistency, leadership, and positive reinforcement. When done right, Sustain ensures that 5S becomes second nature to your team—not something extra, but just "how we do things around here."
Benefits of implementing 5S in your business
Boost in productivity
One of the biggest reasons businesses turn to 5S is for the massive productivity gains it can deliver. By reducing clutter, organising tools, and creating smooth workflows, employees spend less time searching and more time working.
Imagine a production line where every wrench, bolt, and instruction manual is exactly where it should be. Downtime decreases, errors drop, and team output soars. That's not just theory—it's the lived experience of countless companies who've adopted 5S.
Here's how 5S increases productivity:
- Faster access to tools and materials
- Less movement and walking back-and-forth
- Quicker changeovers and setup times
- Fewer interruptions caused by confusion or disorganisation
Improved safety standards
Safety is a critical priority in any workplace, and 5S is a secret weapon for making it a reality. Cluttered environments are accident-prone. Spills, trip hazards, blocked exits—these issues are far more likely in disorganised spaces.
The 5S method helps eliminate these risks in several ways:
- Removing hazards through sorting and cleaning
- Clearly marking safe zones, walkways, and emergency equipment
- Maintaining equipment through routine inspections during the Shine phase
- Standardising procedures that ensure everyone knows how to work safely
But it's not just about preventing accidents. When workers feel safe, they're more confident, more engaged, and more likely to perform at their best. Safety and performance go hand in hand—and 5S supports both.
Reduced waste and costs
One of the most appealing benefits of 5S is its impact on the bottom line. By streamlining operations and eliminating waste, companies often see significant cost savings.
Here's how 5S reduces waste:
- Less inventory waste from expired or damaged goods
- Reduced motion waste from unnecessary walking or searching
- Lower defect rates due to cleaner, more organised workspaces
- Reduced utility costs through more efficient use of space and resources
You'll also spend less on supplies, repairs, and labour because everything is where it should be, working as it should. And when that happens, you get more done with less effort—and more profit at the end of the day.
Enhanced employee morale
A clean, well-organised workplace doesn't just make the job easier—it makes it more enjoyable. Employees notice when their environment is cared for, and that builds a sense of pride and ownership.
Here's how 5S boosts morale:
- Reduces frustration from constantly searching for items
- Promotes team collaboration through shared responsibilities
- Increases job satisfaction by creating a calm, safe atmosphere
- Encourages employee involvement through regular audits and improvements
Better quality control
When your workplace is clean, organised, and standardised, your quality control improves naturally. Mistakes are easier to spot. Defects are less likely to occur. And if something does go wrong, it's easier to trace the problem and correct it quickly.
5S contributes to better quality in several ways:
- Reduces contamination with regular cleaning routines.
- Eliminates confusion with clear labels and standardised procedures.
- Ensures correct tool usage by placing tools in designated locations.
- Improves inspection routines through better visibility and access.
Also, when employees take pride in their space, they naturally pay more attention to detail. That increased attention means higher quality outputs—and fewer customer complaints.
Implementing 5S: a practical guide
Step-by-step implementation strategy
Implementing 5S doesn't have to be overwhelming. In fact, it's best when done in small, consistent steps. Here's a simple implementation strategy:
- Get Leadership Buy-In – Explain the benefits and get management support.
- Form a 5S Team – Include employees from different departments.
- Train Your Team – Make sure everyone understands the 5S principles.
- Choose a Pilot Area – Start small, like a workstation or a room.
- Begin with Sort – Eliminate everything unnecessary.
- Move to Set in Order – Arrange what's left.
- Shine Regularly – Clean and inspect every day.
- Create Standards – Document what works.
- Sustain the Gains – Audit, review, and adjust regularly.
- Scale Up – Once the pilot is stable, expand to other areas.
Common mistakes to avoid
Even though 5S is straightforward, many businesses struggle with implementation. Why? Because they fall into a few common traps:
- Skipping the Sustain phase – Without follow-through, everything falls apart.
- Making it a one-time event – 5S isn't spring cleaning; it's a daily practice.
- Overcomplicating standards – Keep procedures simple and visual.
- Lack of employee involvement – If it's top-down only, it won't last.
- No accountability – Assign roles and review progress consistently.
Tools and software for 5S implementation
While 5S can be done manually, today's technology can make it even more effective. Here are a few tools and apps that help manage 5S practices:
- Trello / Asana: Task assignment and 5S checklists
- 5S Audit Software: Track progress with audit scores
- QR Code Labels: Easy-to-scan locations for tools and inventory
- Digital SOP Tools: Store and share standard operating procedures
- Gemba Walk Apps: Document walk-through observations and feedback
Real-life case studies and success stories
5S in manufacturing
Let's look at a manufacturer that implemented 5S across its factory floor. Before, workers spent up to 30 minutes per shift searching for tools or parts. After 5S, that time dropped to under 5 minutes. They labelled tool cabinets, created shadow boards, and implemented daily cleaning schedules.
The result? A 15% boost in output, fewer machine breakdowns, and happier employees.
5S in offices and service industries
5S isn't just for factories. A marketing firm adopted 5S in their office and digital environment. They sorted and archived digital files, labelled storage cabinets, colour-coded shared workspaces, and cleaned up desktops every Friday.
The benefits? Employees reported higher focus, less frustration, and faster onboarding of new hires. The office felt calmer and more professional, which also impressed clients during visits.
Maintaining 5S over time
Continuous improvement with 5S
5S isn't a destination—it's a journey. To keep the momentum, adopt a mindset of Kaizen, or continuous improvement. Encourage your team to constantly ask:
- What's not working?
- What could be better?
- What's causing delays or frustration?
Conducting regular 5S audits
To make 5S stick, you need a monitoring system. That's where audits come in. Create a simple scoring system and conduct monthly audits in each area.
Checklist items might include:
- Are tools in their proper places?
- Are labels visible and accurate?
- Are cleaning tasks being completed daily?
- Are standard procedures being followed?
Conclusion
5S is more than just a neatness tactic—it's a strategic tool for transforming your business. From reducing waste and costs to boosting morale and safety, the 5S methodology delivers powerful results that ripple through every level of your organisation.
When everyone embraces the principles of Sort, Set in Order, Shine, Standardise, and Sustain, your workspace becomes a place of clarity, pride, and performance. And that's not just good for business—it's great for people, too.
So start small, stay consistent, and let 5S work its quiet magic. You'll be amazed at what your team can achieve when their environment supports their success.
FAQs
Q: What industries benefit most from 5S?
A: While 5S originated in manufacturing, it's now used in offices, healthcare, retail, construction, and even education. Any workspace that needs organisation can benefit.
Q: Is 5S only useful in large businesses?
A: Not at all. Small businesses and startups often find 5S especially helpful because it maximises limited space and resources.
Q: Can 5S be used in remote or hybrid work settings?
A: Yes! Digital 5S can organise cloud files, streamline remote workflows, and keep your virtual workspace clean and efficient.
Q: How long does it take to see results from 5S?
A: Most businesses start seeing results in weeks. Increased efficiency, cleaner spaces, and happier employees show up quickly with consistent application.
Q: What's the best way to train employees in 5S?
A: Use a mix of hands-on workshops, visual aids, and real-world examples. Make it fun and interactive so employees connect with the principles personally.
To find out more about how you can start your own Digital Agency, please contact a member of our team.
Until next time, take care.
Share this Post
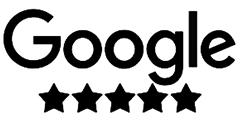
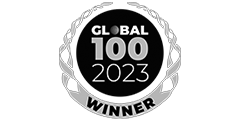



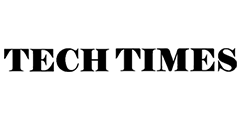

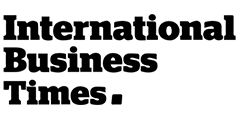